Choosing the Right Equipment for a Cannabis Production Facility
How can you know what the right equipment is for a cannabis cultivation facility build-out? You need to find the right experts to ask- people who have enough experience to know what works, what doesn’t, and aren’t getting kickbacks from the companies they are recommending.
Sadly, the cannabis industry is full of product pushers who make everything sound easy and great, where truly experienced growers will not only have personal experience with most of the cultivation methods and equipment out there, but will also be connected to a network of industry pros they can check with if they need more feedback on any lesser known or up-and-coming companies and products.
Big-Ticket Items
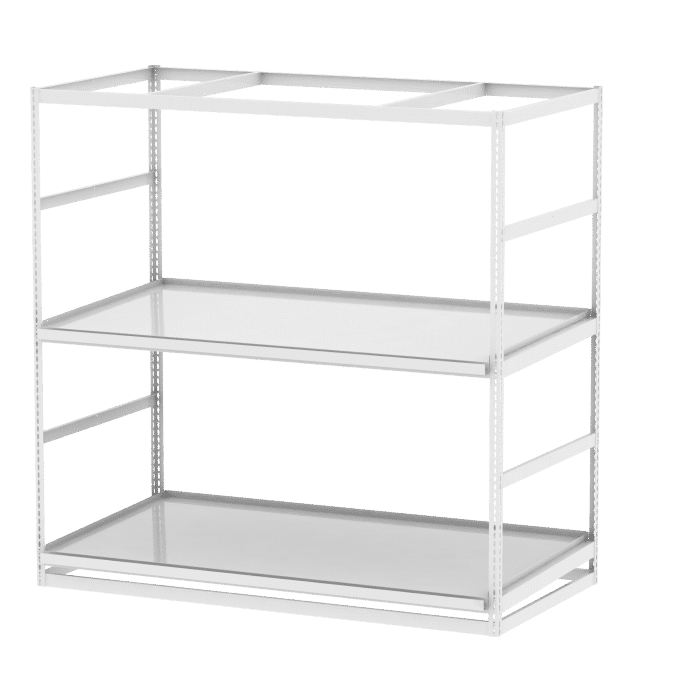
Vertical Rack Unit
Your biggest initial equipment choices will be environmental controls, lights and racks, and the best options will depend on your chosen method of cultivation, your budget and the characteristics of your building.
Just like with anything, the more you spend, the better quality you get, and thus it’s best to find a middle ground where you’ve got a solid reliable system design that doesn’t break the bank.
For two-tier racks, expect to spend at least $1500 per 2-tier 4×8′ rack, installed. Prices can go up to nearly double that for high-end racks with fancy features.
HPS VS. LED Lighting
I started out as an HPS grower on single tier rolling racks on casters and, over time, I’ve moved towards 2-tier vertical LED designs (see my Recent Projects page for images). I made this shift for a few reasons that I’ll list for you:
* HPS lights waste a lot of energy that creates heat but doesn’t promote plant growth.
* HPS lights are somewhat dangerous. The bulbs burn at 1000 degrees and are usually exposed to the open air. Either getting water on them or bumping into one will cause glass breakage and burns.
* HPS lights do not allow for stacking canopies. Most cultivation sites can double their canopy space by using low-profile LEDs in a double stack to make much better use of their floor space.
Of course shifting away from HPS lights required having LEDs evolve to a price and quality level that is workable. Full-spectrum LEDs are now down to about $1000 per 4×4 ft space, usually with considerable additional energy rebates associated, and can produce great quality cannabis with similar yields. You can bump into LEDs and not get burned, you can see plant color clearly under them, and they last a long time with no bulb replacement needed.
For every 1100 watts of HPS light you’d have in a facility, only 650 watts of LED would be needed as a 1:1 substitute. This energy savings is also reflected in your HVAC capital expense and operating cost, because the system can be 35-40% smaller (in tonnage) and equally less energy intensive.
For LED lights, expect to spend $1000 per light (16 sq.ft.) at volumes over 100 lights, and it’s often possible to get another $250-$350 per fixture back from utility rebates.
HVAC & Dehumidification
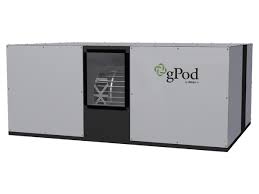
Integrated AC and Dehumidification
When it comes to HVAC and dehumidification, do not follow the advice of growers who only have underground cultivation experience. What we had to do as underground growers would not work in a legal cultivation facility. This is mainly because of the microbial lab test clearance that the legal market requires. Any time a cultivation room has even a short-term humidity spike, mold and bacteria will pile up on the plants and jeopardize their value. Also, badly designed or poorly maintained HVAC equipment quickly spreads pernicious spores throughout a facility.
Let’s take a mini-split system as an example. The blower head that is mounted in the room to be cooled has coils inside that are moist and collect all kinds of microbial growth over the course of just a few months. These blowers are almost impossible to clean and will blast spores all over the room with impunity. The take-away on this is to never have hard-to-clean air blowers or handlers in a plant room.
Another big challenge for cultivation room environmental control is maintaining the humidity at a level that is both consistent and moderate. Plants give off about 1/4 gpd per square foot of moisture as they grow, causing quite a lot of humidity build-up in a room. The classic way that underground growers dealt with this was to place dehumidifiers in the room- as many as it took to drop the moisture levels.
The problem with this approach is three-fold: 1) Just like with AC equipment, the insides of these units get mucked up with mold and can’t easily be cleaned. 2) These machines produce quite a lot of heat that then needs extra AC to offset it. 3) They are often not sized properly to handle the spike in humidity that happens right when the lights go off each night in the flowering rooms, which leads to mold/mildew outbreaks on the plants.
The better method is to use cleanable ducting (whether fabric or metal) inside the plant rooms, and placing all air handlers outside the plant rooms. This way, the machinery won’t be adding unwanted heat to the plant room and the system can be serviced without spitting muck onto the plants.
Keep in mind that your AC system handles a big chunk of the dehumidification requirement of the room (referred to as “latent load” by AC companies and mechanical engineers.) The AC will be sized to offset all of the wattage (heat) that the lights produce, but when the lights go out, there’s no longer a heat load to offset, so the thermostat will turn off the AC and its associated dehumidification. This will result in a problematic humidity spike if the system is designed wrong (and I’ve seen this happen in many many facilities).
Installing an integrated AC and dehumidification system, designed by a company with cultivation facility experience means that you’ll get consistent environmental conditions in the plant rooms during every hour of the day and night.
Back-up Power and Redundancy
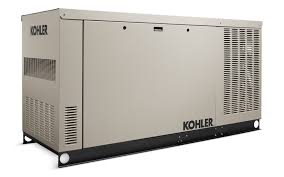
Propane Generator
Any professionally designed cannabis cultivation facility will have back-up power and mechanical redundancy built in. This is pricey, but not in comparison to the loss of losing a crop when (not if) a system fails. You’ll need a back generator that is sized to run your critical lighting, security systems and environmental controls in the event of a power outage.
Backup power costs range depending on how much of the facility is being backed up. Usually, projects only back up ~25% of plant lights, 25% of AC and ~75% of dehumidification. The costs for this are infrastructural and involve electrical engineering and design in order to pre-plan running specific equipment through a particular panel and then an automatic transfer switch to the generator. For design, equipment and installation, expect to spend $100,000 for a small facility, up towards $2mil for a 30k sq.ft. facility.